UAE-based 3D printed footwear startup ELASTIUM has introduced its first fully 3D printed sneakers made from 100% recyclable foam.
ELASTIUM’s sneakers incorporate a novel lattice-structured low-density thermoplastic elastomer (TPE) foam material. This foam is manufactured using ELASTIUM’s proprietary granulate extrusion 3D printing technology. The sneakers prioritize both comfort and resilience, with a softness similar to Crocs and a cushioning capability comparable to high-performance sneakers from popular brands like Nike and Adidas.
“We are thrilled to unveil our world’s first fully 3D printed foam sneakers,” said Robert Karklinsh, Founder, and CEO of Elastium. “Traditional shoe manufacturing is extremely slow, capital-intensive, and unsustainable. 22 out of 23 billion pairs of shoes produced each year end up in landfills, where they may take hundreds of years to decompose. At ELASTIUM, we are redefining footwear production making it rapid, on-demand, localized, and sustainable. We are also democratizing the footwear industry by providing a platform for individual creators and brands which will eventually make footwear production as easy as publishing an app on the App Store.”
Elsewhere, Munich-based startup SNEAKPRINT has launched customized 3D printed shoes manufactured employing conventional craftsmanship in Europe.
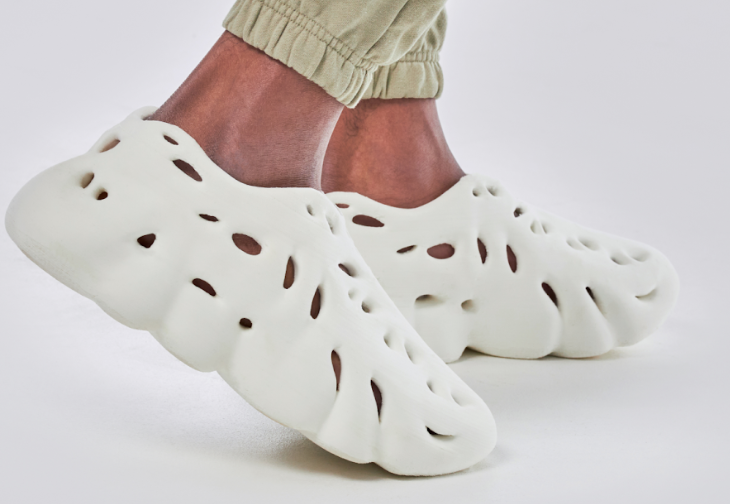
Lightweight, comfortable, and sustainable 3D printed sneakers
ELASTIUM introduces a new method for sneaker production through its fused granulate fabrication (FGF) foam 3D printing technology. This approach utilizes industry-standard raw materials in granule form, enabling superior cost-effectiveness compared to alternative foam 3D printing methods. This technology’s flexibility allows for the printing of multiple materials at varying densities, including both fully dense materials and ultra-lightweight foams with specific gravity as low as 0.14.
ELASTIUM says it differentiates itself from competitors by going beyond the inclusion of 3D printed components in its footwear. It employs high-performance TPU foams in combination with lattice structures, resulting in lightweight, comfortable, durable, and machine-washable 3D printed sneakers that deliver exceptional performance. These sneakers are produced on demand, eliminating conventional manufacturing expenses, reducing carbon emissions, and promoting sustainability.
The “ELASTIUM-1” model stands out with its mono-material design, which was developed through a collaboration between AI and a footwear designer. Looking ahead, ELASTIUM has plans to introduce additional releases and models throughout 2023, offering customers an expanded range of options.
SNEAKPRINT’s custom-fit sneakers
To mark its market entry, SNEAKPRINT introduces the RetroTechV1 sneaker, which draws inspiration from sporty and retro designs. This sneaker is offered in three different variants: a one-color nappa leather option available in black or white, as well as a nappa/suede leather combination in white and gray.
“No two feet are the same, and wearing ill-fitting shoes can cause long-term damage to the feet,” explains Kevin Zürn. Therefore, each sneaker is only available in the “ME-Size” and is individually customized to the customer’s feet.
As part of the process, each new customer is provided with the SNEAKPRINT imprint kit, enabling them to conveniently digitize their feet from the comfort of their own homes. Utilizing this data, SNEAKPRINT develops a precisely fitting midsole that is manufactured using 3D printing. The customized fit and incorporated individual cushioning ensure optimal comfort and help prevent potential foot issues associated with wearing ill-fitting shoes in the long run.
By leveraging 3D printing, SNEAKPRINT is able to produce intricate shapes and structures that are not achievable through conventional manufacturing methods. This approach enables faster and more sustainable production compared to traditional methods. SNEAKPRINT adopts a small-batch production approach and implements print-on-demand strategies, minimizing unnecessary waste by avoiding large pre-printed quantities.

Walking miles with 3D printing
ATHOS, a sportswear start-up based in Spain, launched a collection of 3D printed climbing shoes. According to ATHOS, this introduction marks the first of its kind in the world. These climbing shoes were being developed in collaboration with HP, and Sculpteo, an online 3D printing bureau. Alexandre D’Orsetti, CEO of Sculpteo stated, “Mass customization allows ergonomics that seemed inaccessible in climbing, and ATHOS custom-made slipper fits the foot perfectly providing comfort when climbing.” The ATHOS co-founders agreed that “the benefits of customization and on-demand production help us to deploy a more environmentally responsible consumer and manufacturing model.”
A shoe with a distinct design, inspired by the feet of mythical creatures, was created by German designer and architect Stephan Henrich using 3D printing. This claw-like 3D printed shoe was specifically designed for printing on Sintratec‘s SLS S2 system. According to Henrich, wearing these shoes allows individuals to experience walking in the footsteps of “Cryptids” like Bigfoot or the Loch Ness monster, and “leave behind traces just as these mythical creatures would do.”
Featured image shows Elastium 1 sneakers. Image via Elastium.