Researchers at Princeton University have developed an innovative 3D printing technique that facilitates the production of highly customizable, recyclable soft plastics. This advancement, detailed in Advanced Functional Materials, presents a paradigm shift in material engineering, offering a sustainable and cost-effective alternative applicable across numerous industries, including soft robotics, medical devices, and high-performance sports equipment.
Biomimetic Design and Engineering Precision
In nature, materials derive exceptional properties from intricate hierarchical structures. The durability of nacre, the structural resilience of bamboo, and the iridescence of butterfly wings exemplify the influence of molecular architecture on function. Historically, synthetic materials have struggled to replicate this level of sophistication; however, advancements in high operating temperature direct ink writing (HOT-DIW) are now enabling a comparable level of control in engineered materials.
Princeton’s research team harnessed HOT-DIW to fabricate thermoplastic elastomers (TPEs), a class of nanostructured polymers known for their tunable mechanical properties. As explained by Emily Davidson, assistant professor of chemical and biological engineering, this methodology allows for the precise customization of materials in multiple orientations.
“We can create materials that have tailored properties in different directions,” Davidson stated, underscoring the potential applications of this technology in fields requiring both flexibility and structural integrity.
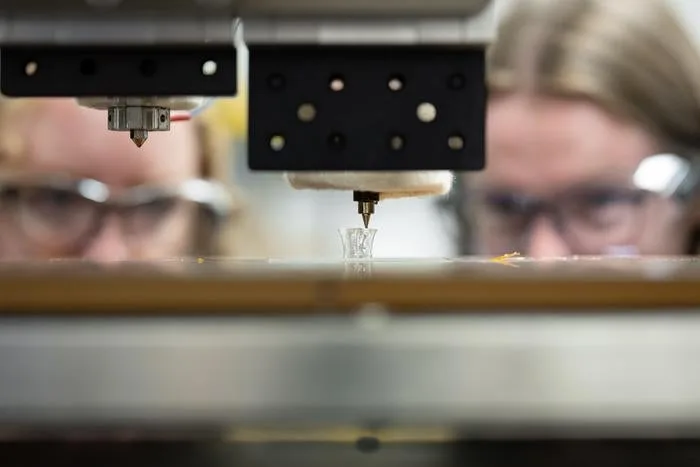
Molecular Engineering and Material Behavior
At the core of this breakthrough lies the molecular architecture of TPEs. These block copolymers feature rigid cylindrical nanostructures embedded in a flexible polymer matrix. The alignment of these nanocylinders, which measure 5-7 nanometers in thickness, during the printing process imparts exceptional mechanical anisotropy, enabling precise control over material properties.
To achieve this alignment, the research team employed controlled shear and extensional flows during HOT-DIW printing. By refining printing parameters, they achieved up to an 85-fold variation in tensile modulus between different orientations of the material—an unprecedented level of mechanical tunability in soft plastics.
Enhancing Performance Through Thermal Annealing
A crucial aspect of this technique is thermal annealing, a controlled heating and cooling process that significantly enhances material performance. Lead researcher and graduate student Alice Fergerson highlighted its dual functionality: “It drastically improves the properties after printing and allows the printed structures to be reused multiple times. It even enables self-healing when damaged.”
Annealing optimizes the nanostructural alignment, resulting in enhanced mechanical properties. Moreover, the self-healing capability of the printed material was demonstrated when a severed sample was seamlessly rejoined through heat treatment, restoring its original mechanical integrity without degradation.
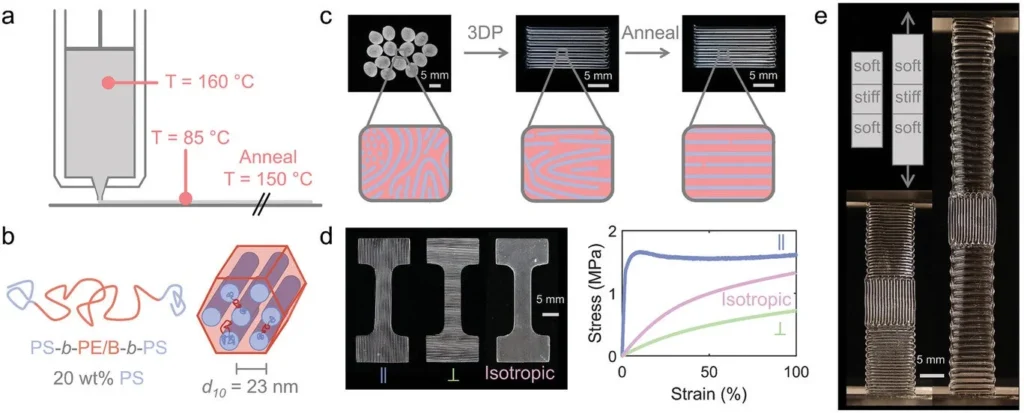
Economic and Environmental Superiority Over Existing Materials
A distinguishing advantage of this approach is its cost efficiency. Traditional liquid crystal elastomers (LCEs), which offer tunable mechanical properties, are cost-prohibitive at approximately $2.50 per gram and necessitate complex, multi-stage processing. In contrast, TPEs cost $0.01 per gram and are compatible with widely available commercial 3D printers, significantly lowering the barrier for industrial-scale implementation.
Beyond cost-effectiveness, TPEs’ recyclability offers a compelling environmental benefit. Unlike chemically cross-linked elastomers, TPEs can be reprocessed via melting without material degradation. Additionally, the research team successfully integrated functional additives—such as an organic molecule that causes the plastic to fluoresce under ultraviolet light—demonstrating the material’s potential for applications in wearables, sensors, and smart materials.
Broad Implications for Advanced Manufacturing
The implications of this research extend across multiple disciplines. In soft robotics, materials exhibiting both flexibility and durability could facilitate the development of more responsive and adaptive robotic systems. Similarly, customized medical devices and prosthetics could be tailored with greater precision to meet individual patient needs. Furthermore, high-performance sports equipment, such as helmets and footwear, could be engineered for superior shock absorption and wear resistance.
To showcase the precision of their 3D printing process, the Princeton team fabricated intricate structures, including a miniature plastic vase and the word “Princeton” rendered in a complex, sharply defined design. These examples underscore the technique’s ability to produce geometrically sophisticated and mechanically robust materials.
Future Research Directions
The researchers aim to further refine this technology by developing new printable architectures optimized for wearable electronics and biomedical applications. Additional studies will explore the integration of conductive and sensing materials, expanding the functional capabilities of TPE-based structures.
By leveraging fundamental insights into polymer physics alongside advanced manufacturing techniques, the Princeton team has successfully created a scalable, cost-effective, and sustainable material solution. As industries increasingly prioritize sustainability and efficiency, innovations such as this could redefine material design and manufacturing standards.
With its capacity to produce durable, recyclable, and precision-engineered soft plastics, this technological breakthrough holds immense promise for revolutionizing multiple sectors, including healthcare, robotics, and consumer goods.
Sources:
- Princeton University Research
- Advanced Functional Materials
- The Brighter Side of News (Content adapted for style and clarity)